Ever felt like you’re stuck in a never-ending waiting game with suppliers? You place an order for a custom wood sign, and it feels like watching paint dry—or worse, waiting for grass to grow. We’ve all been there, frustrated with delays and empty promises. The clock’s ticking, and your project can’t wait forever. So what’s the real deal with production times, and how can we speed things up?
Typically, making a custom wood sign takes anywhere from two to four weeks from start to finish. This timeframe includes design approval, production, and shipping. However, if you’re working with a responsive supplier who has streamlined processes and adequate inventory, you might get your custom sign even sooner. Factors like complexity of design, size, and current workload can affect the timeline, but a good supplier will keep you in the loop every step of the way.

What Factors Affect the Production Time of Custom Wood Signs?
Several factors can speed up or slow down the process. Let’s break it down:
Design Complexity
When it comes to custom wood signs, not all designs are created equal. A simple sign with straightforward text and minimal graphics can be produced much quicker than an elaborate piece with intricate carvings, multiple layers, and detailed artwork. Think of it like ordering a pizza: a plain cheese pizza comes out faster than one loaded with every topping under the sun.
Complex designs can add anywhere from 3 to 7 days to the production time. So if you’re in a hurry, you might want to keep it simple—or at least be aware that more elaborate designs will take a bit longer.
Size of the Sign
Size matters—at least in terms of production time. Larger signs require more materials, more time to assemble, and often more hands on deck to handle the project. If you’re ordering a massive sign to hang on the side of a building, expect that it will take longer than a small plaque for your office door.
As per industry stats, signs over 3 feet in length can increase production time by up to 25%. So plan accordingly if you’re going big.
Current Workload
Ever tried to get into a popular restaurant without a reservation? Suppliers can be the same way. If they’re slammed with orders, your project might get pushed down the queue. That’s why it’s crucial to discuss timelines upfront.
Suppliers with efficient workflow management can juggle multiple orders without significant delays. But beware of those who overpromise and underdeliver. A quick chat about their current workload can save you a lot of headaches down the line.
Inventory Levels
Imagine ordering a custom suit only to find out the tailor has to wait for fabric to arrive. Similarly, if a supplier doesn’t have the necessary materials in stock, it can delay your order. Suppliers with robust inventory levels can kick off your project immediately, whereas those who need to source materials might take longer.
Finishing and Treatments
Additional finishes like staining, painting, or weatherproofing can add time to the production process. These steps often require drying or curing times, which can’t be rushed without compromising quality.
For example, applying a high-quality varnish might add 2-3 days to the timeline, according to finishing experts.
Shipping Time
Ah, shipping—the final frontier. You’d think once the sign is made, it’s smooth sailing, but shipping can be a wild card. Factors like distance, shipping method, customs (for international orders), and even weather can affect delivery times.
For international shipping times, especially from China to the US, air freight typically takes 7-10 days, while sea freight can take 30-40 days.
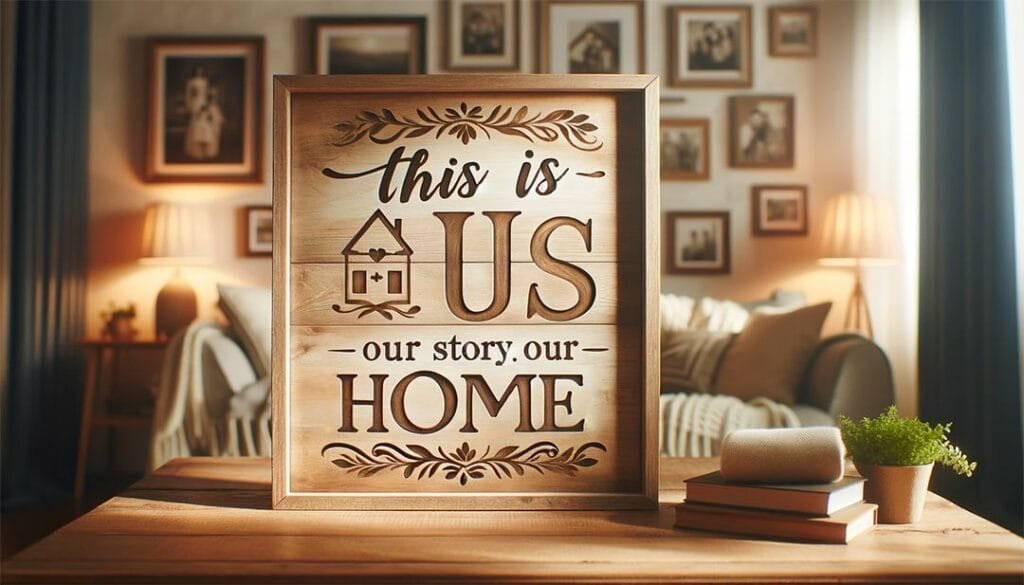
How Can You Speed Up the Process?
Now that we’ve covered what can slow things down, let’s talk about how to put the pedal to the metal.
Clear Communication
The importance of clear, concise communication can’t be overstated. From the moment you place your order, make sure all your specifications are laid out. Provide detailed drawings, measurements, and any other pertinent information.
Misunderstandings lead to revisions, and revisions lead to delays. As they say, “Measure twice, cut once.” Or in this case, “Communicate clearly, produce swiftly.”
Choose the Right Supplier
Not all suppliers are created equal. Look for ones with a reputation for quick turnaround times and stellar customer service. Read reviews, ask for recommendations, and maybe even test them with a small order first.
A supplier who understands the importance of deadlines and goes the extra mile to meet them is worth their weight in gold—or in this case, wood.
Approve Designs Quickly
Time is of the essence when it comes to approving design proofs. The faster you give the green light, the sooner production can begin. Keep an eye on your email, and don’t let that approval request sit in your inbox while you’re binge-watching your favorite show.
Opt for Standard Materials
While exotic woods and unique finishes can make your sign stand out, they can also add significant time to the production process. If you’re in a hurry, consider using standard materials that are readily available. You can still achieve a great look without the added wait.
Consider Expedited Shipping
If time is really tight, opting for expedited shipping can shave off days, if not weeks, from your delivery time. Be prepared to pay a bit more, but sometimes the convenience is well worth the extra cost.
Frequently Asked Questions
Can I Get a Custom Wood Sign Made Faster If I Pay Extra?
In many cases, yes. Some suppliers offer rush services for an additional fee. This could reduce production time by 20-30%, depending on the supplier’s capacity. It’s like upgrading to first class—you get to skip the line.
Always check with your supplier to see if this is an option. Keep in mind that rushing the process shouldn’t compromise the quality of the final product.
What’s the Typical Shipping Time from China to the US?
As mentioned earlier, shipping times can vary. Air freight is faster but more expensive, taking about 7-10 days. Sea freight is more economical but slower, clocking in at 30-40 days.
Do Suppliers Offer Confidentiality Agreements?
If you’re concerned about protecting your unique designs or business information, many reputable suppliers do offer confidentiality agreements. This ensures your designs won’t be shared or reproduced without your consent.
Always discuss this upfront and make sure both parties sign off.
How Does the Time of Year Affect Production Times?
Believe it or not, the time of year can impact production schedules. Holidays, both in your country and the supplier’s, can cause delays. For example, Chinese New Year is a major holiday where factories may shut down for up to two weeks.
What If There Are Delays?
Delays can happen despite everyone’s best efforts. The key is communication. A good supplier will notify you promptly about any issues and provide solutions or adjusted timelines. Always have a contingency plan if your project is time-sensitive.
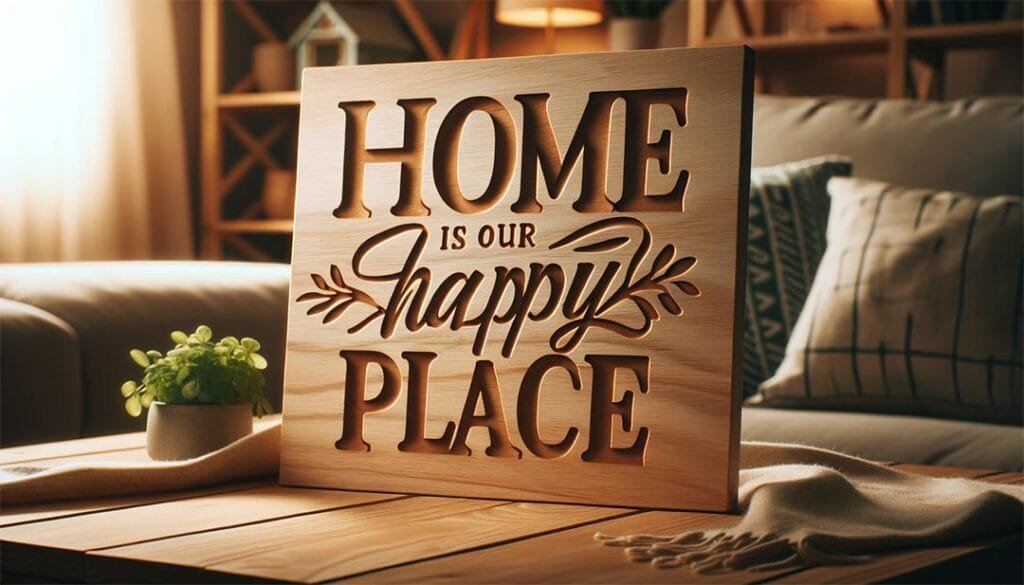
The Bottom Line
Navigating the world of custom wood sign production doesn’t have to be a maze. By understanding the factors that affect production time and taking proactive steps, you can significantly streamline the process. Remember, a typical timeframe is two to four weeks, but with the right approach, you might just beat the clock.
As someone who’s been in the biz for a while, I get the frustrations of delays and the impact they can have on your projects. That’s why I’m committed to making the process as smooth as possible for folks like you.
Conclusion
So, there you have it—the ins and outs of how long it takes to make a custom wood sign. With a bit of planning and the right partner (hint: that’s me), you can get your hands on that perfect sign without the wait feeling like an eternity. Ready to make your vision a reality? Let’s get the ball rolling!